HDN
Well-known member
- 2,103
- 5,061
- 113
- Location
- Finger Lakes Region, NY
This fellow wasn't wrong when he said packing the M35A3's inner wheel bearings in this manner was time-consuming, so I printed a tool to speed up the process.After doing some research I found the bearings are not only very expensive but the inner bearings are packed at the factory by timken and the inner seal is part of the bearing and not available separately. I suppose if the seal fails the bearing is meant to be replaced. With inner bearings in the 800$ each range I decided to try to clean the seals and repack them and since there is not suppose to be diff oil in the bearings any way I would order new outer seals to keep the diff oil out of the bearings. I have attached a series of photos of the process, it seems the bearings, with the CTIS system, include bezzels that are part of the inner bearing race and protrude into an air seal in the inboard hub. The inner grease seal is driven (metal to metal seal) into a small lip that is machined into the outer bearing race with the inner part of the seal (also metal to metal seal) is driven onto a small lip machined into the inner race. I was conserned about damaging the seal by driving it off of the inner race so I left it attached to the race and packed the bearing from the inner side (sort of time consuming) then applied a light layer of aviation permatex to the outer perimeter of the seal and gently drove it back into the outer race.
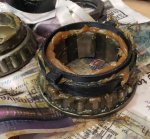
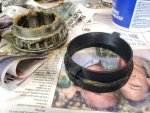
My tool forces grease into the ~1.5 mm gap between the cage and inner race, forcing all the old gunk out from above the rollers and through the bottom gap between the cage and the lip that's driven onto the bearing.
I printed this with black ABS plastic (the same plastic Lego bricks are made from). I printed the tool in about 3 hours.