@silverstate55 @98G Thanks for the input

I do have an issue that I am going to need to solve the long, hard way by tearing the whole thing back apart or maybe a few attempts at the easy way.
The issue is this new pressure plate, as stated above, was adjusted and installed to the same height as the pressure plate I took out. However when testing the clutch engagement/disengagement I found that the throw of the linkage total moves the throw out bearing lever arm 1.085" when pressed. This distance is just barely not enough distance to have full release of the clutch and still have full "release" of the throw out bearing to ensure it isn't spinning when driving down the road, or idling. Since I was in a rush to be able to make the parade I just went with disengagement as my priority, Ahhh yes shifting with syncros that work was so nice, but I need to get this corrected ASAP as I don't want to eat up another throw out bearing and have to do this all over again.
So three things to solve here:
1. Get full needed travel of the fork arm go get full throw out release and get full clutch engagement/disengagement.
2. Get the clutch not to "chatter" Which I am still getting with this clutch and pressure plate which I am guessing is that the entire motor/trans shifts as torque is applied and gives the clutch chatter on engagement with the mechanical linkage from the body to the frame to the transmission flexing, as it doesn't seem to be related to RPM when engaging the clutch. If this chatter is not related to the "play" in the engine/trans mounts and is related solely to the pressure plate there is nothing that will fix it except tearing everything apart and again, using a micrometer and measure the height of everything as I adjust the pressure plate. However I did all this checking/adjusting when I put it in this time so I feel confident that this is not my issue... please don't be the issue.... LOL.
3. Solve the binding flex issue I get when wheeling when I can't get the clutch to release when in a serious frame flex.
The possible solution to all of these is a hydraulic clutch. Knowing I will need over 1.1 inches of travel makes me a bit worried but maybe it will all work out.
This Wilwood clutch assembly pictured below has a 1.38 stroke which may solve my 1st issue due to the increase stroke. The 2nd issue would be solved due to the motor and transmission not "torquing rolling" physical linkage in the frame and the 3rd issue similar to the 2nd would be solved when the frame no longer flexing the linkage between the body and frame as well as the frame to the transmission. I will be looking on how it would mount as they do have several options there. (there are several single output master cylinders available to ensure that the maximum travel can be had out of the slave cylinder). The one in the picture may not work as the slave has a .60 cubic volume and this master pictured says it only has a travel of 1.2" at 7/8" diameter with a volume of .55 which is not enough. I am thinking something with at least .60 + just a bit for the flex in the line going down to the peddle. The High Volume single output master cylinder that has a 3/4" piston and a 1 7/8" travel that has .62 cu/in of volume would be the ticket. This will also get me back the loss in lever arm advantage and actually get me a slightly softer peddle due to it adding a 36% hydraulic mechanical advantage.
Did a bit of checking, currently the peddle moves 9" down to the floor. to create 1.085" of motion to the clutch lever arm. Basically 9" to 1.1". The Wilwood peddle here is a 7:1 so my peddle with it would be stiffer by 29% according to Google AI assistant. With the hydraulic advantage but longer throw of the peddle I could get a softer peddle overall but with a longer throw.
As I was taking these measurements I noticed I could get about 1 more inch out of my current peddle travel. I will try that first but should only get me to 1.205" on the lever arm, but maybe it is enough. If so then the Wilwood clutch would definitely be a solid solution.
Update:I made a cardboard cut out of the Wilwood peddle and it would definitely work inside of the cab. In fact it is excellent. I would later buy a 2nd peddle for the brake Hydro max system. The way it would work is there is a "pair of vertically placed but slightly diagonal pates that run from the firewall to the dash to give the steering wheel full support. I would make a bracket to bolt into that "fin" for the top two bolt mounts on the peddle and then bolt the firewall side as well. The firewall is a bit wavy at that particular section but I would either clamp it or bridge the space to ensure a solid fit. This way the clutch and brake are near centered around the steering wheel. It would also give the peddle for the clutch a press forward feel rather than a stomp down feel as your pressing it which is more natural to me.
I need to verify what is on the backside of the firewall at that point but I think it is only the resistor and the relay box which I could scootch to one side or the other to make this solid.
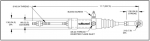
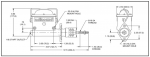
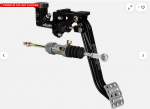