Boi
New member
- 19
- 9
- 3
- Location
- Saint Charles, IL
Hello all,
It has been a been quite an interesting endeavor, but the work is finally complete. The transmission for my M923A2 has been resurrected from the dead by my father and I, repaired on the side of a public road, with little more than a box of tools. I figured I should post the journey here, so that others may benefit from the experience.
A little background:
I acquired my M923A2 about a year and a half ago and drove it about 400 miles from New Jersey to Virginia. After almost exactly one year of owning it and driving it around 15 miles once a week, the transmission kicked the bucket. I was cruising along doing about 45mph when the truck shuddered, went into neutral, came back, and finally stayed in neutral. The truck was able to move in reverse, but not forward; it was later found out it could move forward if given enough gas.
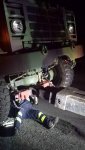
Truck getting towed.
The diagnosis:
The forward clutch is engaged for all forward gears, so with no forward gears the forward clutch seemed like the culprit. Pressure measurements were taken and all looked fine. With good pressure, it seemed somewhat unlikely that the clutch failed, so perhaps it was the centrifugal check-valve in the forward clutch housing that had failed and was bleeding off pressure to drive the forward gears. This was also an incorrect hypothesis and was only discovered when the transmission was disassembled. The valve body was pulled and examined, and passed inspection. The only thing left was to pull the transmission. It became very obvious what the problem was as soon as the transmission came out: the forward clutch turbine shaft completely snapped in half. Apparently this is a common problem with the MT654CR transmission.
The removal:
During the removal of the transmission, there were two of things that proved invaluable to our success: a Harbor Freight half-ton lift table and a wooden transmission support frame. The transmission weighs over 700lbs, so this is not something you can just bear-hug out of the truck.
Armed only with two toolboxes full of 1/4" to 1/2" ratchets, sockets, extensions, combination wrenches, a 3/8" 10-75 ft-lb torque wrench, a small pry-bar, and a crescent wrench, my father and I were able to pull the transmission in a day, and later reinstall it in less than a day. This is definitely a two-man job, as there were several instances of requiring someone to move/hold something while the other turns wrench or visually monitors things while removing/installing components.
During tear-down I never went any further than the 4th clutch, partially because it wasn't necessary, and partially because a total tear-down would require removal of a 3" self-locking nut on the output yoke that is torqued to 600-800 ft-lbs (seen in step 8 of removal). In any case, the repair was fairly straightforward. The parts used for repair were sourced from Trans Machine in Aurora, IL. They have a large warehouse of re-manufactured parts, serviced by an even larger machine-shop in the back. The folks there were very helpful and friendly and their parts were reasonably priced.
It has been a been quite an interesting endeavor, but the work is finally complete. The transmission for my M923A2 has been resurrected from the dead by my father and I, repaired on the side of a public road, with little more than a box of tools. I figured I should post the journey here, so that others may benefit from the experience.
A little background:
I acquired my M923A2 about a year and a half ago and drove it about 400 miles from New Jersey to Virginia. After almost exactly one year of owning it and driving it around 15 miles once a week, the transmission kicked the bucket. I was cruising along doing about 45mph when the truck shuddered, went into neutral, came back, and finally stayed in neutral. The truck was able to move in reverse, but not forward; it was later found out it could move forward if given enough gas.
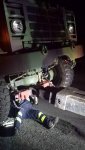
Truck getting towed.
The diagnosis:
The forward clutch is engaged for all forward gears, so with no forward gears the forward clutch seemed like the culprit. Pressure measurements were taken and all looked fine. With good pressure, it seemed somewhat unlikely that the clutch failed, so perhaps it was the centrifugal check-valve in the forward clutch housing that had failed and was bleeding off pressure to drive the forward gears. This was also an incorrect hypothesis and was only discovered when the transmission was disassembled. The valve body was pulled and examined, and passed inspection. The only thing left was to pull the transmission. It became very obvious what the problem was as soon as the transmission came out: the forward clutch turbine shaft completely snapped in half. Apparently this is a common problem with the MT654CR transmission.
The removal:
During the removal of the transmission, there were two of things that proved invaluable to our success: a Harbor Freight half-ton lift table and a wooden transmission support frame. The transmission weighs over 700lbs, so this is not something you can just bear-hug out of the truck.
Armed only with two toolboxes full of 1/4" to 1/2" ratchets, sockets, extensions, combination wrenches, a 3/8" 10-75 ft-lb torque wrench, a small pry-bar, and a crescent wrench, my father and I were able to pull the transmission in a day, and later reinstall it in less than a day. This is definitely a two-man job, as there were several instances of requiring someone to move/hold something while the other turns wrench or visually monitors things while removing/installing components.
1. The first step was draining all the fluid and dropping the pan. The cross-member must be removed first. For any transmission diagnosis, this is almost always the first step as you can see whether there are chunks of metal, bits/flakes of metal, or clutch material in the bottom of the pan, which will help guide your diagnosis. For my truck and this particular failure, it was little bits/flakes of metal.
- Remove the cross-member which passes under the transmission. This requires the fuel filter canister in the left wheel-well to be detached. The canister can be left to hang.
- Disconnect the dip-stick tube. This is attached to the engine on the right side, just inside of the right motor-mount, near the starter. It is held by a bolt which also holds a circular cover. This cover can be removed, as it will provide access to the bolts which hold the torque converter to the ring gear. The fluid will flow nicely out of the hole where the dip-stick tube was located. If the fluid flows slowly due to vacuum, you can open up the PTO plate on the right side of the transmission.
Pan with fluid and metal bits.
Metal bits found in the pan.
2. The valve body was removed and inspected for broken springs, missing check balls, and damaged valves. Everything was OK.
Valve body assembly.
Fluid/pressure channels on transmission housing.
Valves and springs. Color codes are for different spring constants. You can adjust shift points by rotating the 'stepped spacers'.
3. The forward propeller shaft was disconnected from the front axle and left to dangle to the side. It is not necessary to disconnect the propeller shaft from the transfer case. The propeller shaft is attached by a flange with nut+bolts.
4. The propeller shaft between the transmission and the transfer case was removed. This propeller shaft is connected by a set of 8 bolts, a set of 4 on each side, 2 on each on the u-joint.
5. All extraneous assemblies were removed from the transmission. This includes: shift linkage, fluid lines, to/from-cooler lines, and modulator actuator. There was a plastic vent hose on the very top left side of the transmission that was left until the transmission was fully dropped. The to-cooler line on the top of the transmission has a temperature sensor attached to it. Be sure to disconnect the wires and remove the sensor+hose together. It was in this hose, stopped by the temperature sensor, that a collection of needle bearings was found.
Needle bearings recovered from the to-cooler line.
6. Using measurements from the base of the transmission to the ground, a wooden support frame was constructed so as to keep the transmission at the same angle it was when installed in the truck. This was to minimize headache when it came time to reinstall the transmission. The wooden support frame was then raised to support the transmission using the lift table. The rear transmission support was removed, leaving just the bolts to the engine.
Transmission supported by lift table and wooden support frame.
7. It is through the hole that was covered by the circular cover removed earlier (w/dipstick tube) that the bolts connecting the torque converter to the ring gear must be removed. A thin-walled socket is a MUST. Some engineer thought it was a good idea to make the relief just a hair too small for regular sockets to remove these bolts. There are 12 bolts around the edge of the ring gear. What we did to remove the bolts was open an access hole on the rear-left side of the engine. It was through this hole that you could see the teeth on the ring gear that the starter engages. Using a small pry-bar, the ring gear was rotated until a bolt was visible in the hole on the other side of the engine. All these bolts were removed, leaving only the bolts which hold the transmission to the engine.
A bolt connecting the ring gear to the torque converter visible through the hole.
8. The bolts connecting the transmission to the engine were then removed, and the transmission was then free to be lowered out of the truck. The plastic vent-hose was then removed. IMPORTANT: be sure to strap the torque converter to the transmission so it does not fall off! The torque converter weighs something greater than 150 lbs.
Transmission removed. The plastic vent-hose is visible at the top left.
9. The transmission was now completely free. The torque converter was then removed; this is a very heavy object, with very little to hold on to. A two-person lift is highly recommended.
Transmission out of the truck.
Torque converter. Boot for scale.
10. At this point, it was obvious that the turbine shaft was broken. Once the torque converter was removed, the shaft was lying "limp" in the front support assembly.
Broken turbine shaft.
View inside the front support assembly, converter ground sleeve. Shaft is the forward clutch turbine shaft.
The repair:During tear-down I never went any further than the 4th clutch, partially because it wasn't necessary, and partially because a total tear-down would require removal of a 3" self-locking nut on the output yoke that is torqued to 600-800 ft-lbs (seen in step 8 of removal). In any case, the repair was fairly straightforward. The parts used for repair were sourced from Trans Machine in Aurora, IL. They have a large warehouse of re-manufactured parts, serviced by an even larger machine-shop in the back. The folks there were very helpful and friendly and their parts were reasonably priced.
Transmission and torque converter loaded into the bed of a pickup for transport.
1. The first thing broken down was the torque converter (after being drained). There are several pieces in the torque converter, and each was inspected for damaged and the fluid sifted to check for pieces of needle bearings. Everything looked fine, but it looked like the torque converter was already serviced in the past due to turbine shaft failure. The evidence was scoring on the lockup piston, a gouge on the internal splines for the turbine, scoring around the edge of the stator, and a dent on the edge of the pump. The torque converter was reassembled, only repairing the dent in the pump.
Torque converter opened.
Scoring on lockup piston.
Damage to turbine splines.
Dent on pump.
2. The pump on the transmission was rather tricky to remove. This required heating the outside of the transmission housing with a heat gun and pulling on/tapping on the converter ground sleeve on the front support assembly. This takes patients and a careful hand as there is a seal around the edge of the pump; the entire assembly is almost an interference-fit to the housing. The pump was then separated from the front support assembly and inspected for damage and metal bits. Again, no bits or damage were found, but the front support assembly needed to be replaced due to damage to the seals and converter ground sleeve.
Pump assembly.
Last edited: