Back in February a non-running MEP-803a and MEP-802a came up for auction locally. I've always wanted an -803a after owning two -802a's. The -803a was missing its exhaust flapper, making me hesitant to bid on it and after asking around here, I was more hesitant. I looked carefully at the photos and didn't see any indications of water running out of the exhaust manifold. (or wet-stacking) It was missing several switches and had some cosmetic damage, but otherwise looked like a nice unit.
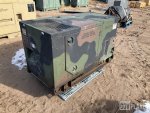
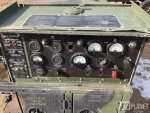
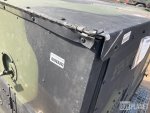
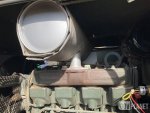
I figured if it was a dud, I would take the hit and either rebuild the engine or part it out. My logic being, this is Colorado and we are typically very dry, so the chance of water filling the engine was low. Auction day came and it must have been slow around here because I picked it up for the minimum bid, $1100, not having to fight anyone else for it!
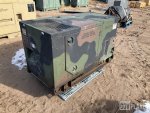
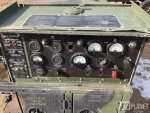
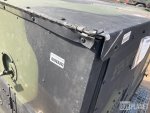
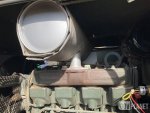
I figured if it was a dud, I would take the hit and either rebuild the engine or part it out. My logic being, this is Colorado and we are typically very dry, so the chance of water filling the engine was low. Auction day came and it must have been slow around here because I picked it up for the minimum bid, $1100, not having to fight anyone else for it!
Last edited: