Some years ago I owned a 1986 Ford Ranger XLT with the off-road package. I wanted an air horn in it, and this is how it was done.
I sourced the air horn from a steel scrapyard, it was attached to the roof of a semi-tractor body that had been scrapped. I also bought the dual-needle air pressure gauge from inside the cab as well.
The horn was about 3’ long. It was fitted with the edge of the business end in front of a hole in the radiator core support, and the back was almost to the firewall. By the way, I didn’t drill a single hole anywhere for any of the components- I fabbed up brackets to existing holes or fasteners.
I found a small aluminum tank, about 1 to 1½ gals I guess, and mounted that up under the right rear wheel well.
I used a 12v cheap compressor mounted to the inside of the left front fender, under the hood. All the plastic body parts of the compressor were removed.
It was plumbed thusly; A toggle switch on the dash energized the compressor which charged the tank, (air-brake lines and fittings) using a check-valve to keep the tank pressurized. A T fitting on the tank side of the check-valve fed one needle on the gauge, another T fitting before the check-valve fed the other needle to tell compressor pressure. So when the tank needed recharging, one needle had the tank pressure, the other needle was at zero. When the compressor was turned on, the one needle would rise until it met the tank pressure needle, and then they’d move up together until the tank was full. At that point I had a manual unloading valve to dump the compressor side pressure (compressor couldn’t restart if there was pressure left).
I had an electric solenoid air valve to dump tank pressure to the horn, with a push-button switch on the gearshift lever (since that was where my hand was usually resting. I also wired it to one of the aux outputs of the alarm system, so I could blow the horn from far away.
That horn was
LOUD too. I stripped it all out before I sold the truck, so it’s all in a box somewhere around here…
EDIT to add: I don't think the whole mess cost me more than $60 to $80 at the time.
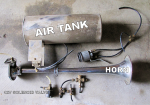
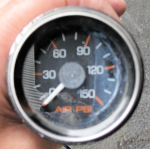