- 147
- 282
- 63
- Location
- NC
I have a 2002 M1078A1 (really an A0.5 since no batt disconnect and has the Polarity Protection Device vs the Load Balancing Battery Control Device). I have been investigating my PPD and battery cables due to age and an intermittent D1323 ( ECU INPUT VOLTAGE HIGH ) "CHECK TRANS" that will sometimes illuminate at highway speeds after 20-30mins, sometimes not, but always extinguishes once I come to a stop. My PPD was connected during all of this.
I'm considering eliminating the PPD while I re-make the battery tray/box, but could it be providing reverse current protection to the batts/alternator (top post of PPD) ? And/or could it be suppressing voltage spikes (kind of via mis-use, since that is the purpose of capacitors) from cab components turning on/off ?
I am fairly familiar with how diodes work, and have found some shottky diodes (preferred for low forward voltage drop) that seem like they could be used to replace the PPD if placed inside the cab near the PDP ?
My PPD has seen better days. Studs are extremely rusted, and the top post might have twisted when I was removing the nut (I used a wire brush to knock rust off, let penetrating oil sit for 15mins+, and re-applied penetrating oil a few times to try and avoid this twisting. It either twisted in the middle of the stud, attempting to shear off, or twisted entirely in the base). I'm going to wire wheel the **** out of it and do some tests on my bench setup with multimeter, but it seems like this will only be more and more difficult to find. And was a pain to even get to.
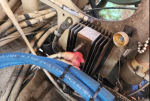
I found some commercially available diodes I think might be decent in-cab replacements:
220CMQ030, which is a 30V 110A diode *pair*. Aside from having an extraneous input and an overly spec'd amp rating, seems pretty ideal. Could easily be mounted on a heatsink, but I *doubt* there's anywhere near 50A of 24v or 12v going into the cab despite the relays being rated for that on the back of my PDP... Two of these would be about $140 shipped, similar in cost to the used, unknown condition/untested, PPDs I see on eBay. 1/4-20 screw mounted (similar in size to M6, for future reference).
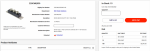
There are cheaper ones like this VS-T70HFL20S02, rated at 70A and 200V. Would probably fit pretty well behind the PDP and uses M5 screws (0.19")
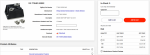
There are double parallel diodes like this SK2S120-100, but it mounts with M4 screws (0.15")... which seem vastly undersized to interface with the 4-6AWG cabling I've seen behind the PDP ? Otherwise, 60A per diode, 100V max, seems reasonable.
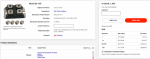
Or this Amazon special LCLCTC 200A one, which I'm hesitant to use due to the terrible description but it appears to be a generic MD250 alieexpress/alibaba diode which have datasheets available. Mounts with M6 (or the 100A version mounts with M5). The only written review for this just expresses displeasure with the description being poorly translated. The 100A version has many other reviews, and this is just a generic diode sold under a dozen different names.
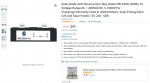
It seems like the PPD could then be upgraded to an LBCD with a Victron BatteryProtect 100A (or the "smart" bluetooth version Victron Energy Smart BatteryProtect 100A). Could anyone think of why this would, or wouldn't, work ? Batt/Alternator cable combined with cab 12 or 24v cable -> Battery Protect -> Diode -> PDP ?
It is a shame the battery protect doesn't incorporate a diode into it.
Danger Reverse Current when using Battery Protect for charging - Victron Community (victronenergy.com)
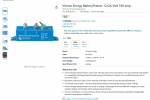
Thoughts ?
I'm considering eliminating the PPD while I re-make the battery tray/box, but could it be providing reverse current protection to the batts/alternator (top post of PPD) ? And/or could it be suppressing voltage spikes (kind of via mis-use, since that is the purpose of capacitors) from cab components turning on/off ?
I am fairly familiar with how diodes work, and have found some shottky diodes (preferred for low forward voltage drop) that seem like they could be used to replace the PPD if placed inside the cab near the PDP ?
My PPD has seen better days. Studs are extremely rusted, and the top post might have twisted when I was removing the nut (I used a wire brush to knock rust off, let penetrating oil sit for 15mins+, and re-applied penetrating oil a few times to try and avoid this twisting. It either twisted in the middle of the stud, attempting to shear off, or twisted entirely in the base). I'm going to wire wheel the **** out of it and do some tests on my bench setup with multimeter, but it seems like this will only be more and more difficult to find. And was a pain to even get to.
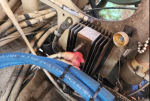
I found some commercially available diodes I think might be decent in-cab replacements:
220CMQ030, which is a 30V 110A diode *pair*. Aside from having an extraneous input and an overly spec'd amp rating, seems pretty ideal. Could easily be mounted on a heatsink, but I *doubt* there's anywhere near 50A of 24v or 12v going into the cab despite the relays being rated for that on the back of my PDP... Two of these would be about $140 shipped, similar in cost to the used, unknown condition/untested, PPDs I see on eBay. 1/4-20 screw mounted (similar in size to M6, for future reference).
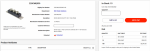
There are cheaper ones like this VS-T70HFL20S02, rated at 70A and 200V. Would probably fit pretty well behind the PDP and uses M5 screws (0.19")
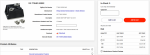
There are double parallel diodes like this SK2S120-100, but it mounts with M4 screws (0.15")... which seem vastly undersized to interface with the 4-6AWG cabling I've seen behind the PDP ? Otherwise, 60A per diode, 100V max, seems reasonable.
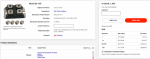
Or this Amazon special LCLCTC 200A one, which I'm hesitant to use due to the terrible description but it appears to be a generic MD250 alieexpress/alibaba diode which have datasheets available. Mounts with M6 (or the 100A version mounts with M5). The only written review for this just expresses displeasure with the description being poorly translated. The 100A version has many other reviews, and this is just a generic diode sold under a dozen different names.
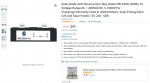
It seems like the PPD could then be upgraded to an LBCD with a Victron BatteryProtect 100A (or the "smart" bluetooth version Victron Energy Smart BatteryProtect 100A). Could anyone think of why this would, or wouldn't, work ? Batt/Alternator cable combined with cab 12 or 24v cable -> Battery Protect -> Diode -> PDP ?
It is a shame the battery protect doesn't incorporate a diode into it.
Danger Reverse Current when using Battery Protect for charging - Victron Community (victronenergy.com)
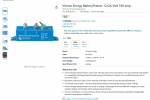
Thoughts ?
Last edited: