- 2,499
- 6,068
- 113
- Location
- Portland, OR
My engine mounts were shot. And every other truck I've looked at was in similar condition. Speaking with someone in the know - apparently even Acela doesn't change these.
2008 M1079 w/25,000 miles.
Before. You can see the "fretting" from vibrations that is causing that characteristic red "dusty" look. That's from constant abrasion of the metal that is shedding bits of iron and abrading the oxide layer. You can also see some cracking where the rubber is delaminating from the steel plates.
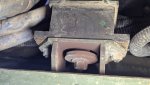
You can see that the safety sleeve that protects the bolt is eating it's way into the frame mounting bracket:
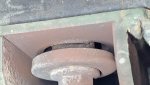
Changing these involves taking the upper fan shroud loose, unbolting the mounts, then lifting the engine up. I could only get about 1.5-2", and unlike the TM's suggestion of "remove the mounts" I had to unbolt the frame mounting bracket lower bolt, and loosen the upper bolt to rotate the bracket and allow removal of the rubber mount, sleeve, and bolt.
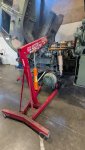
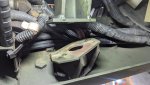
Old mounts and sleeves:
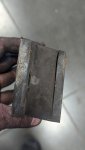
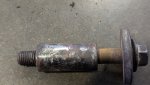
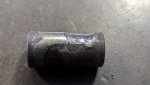
New mount installed:
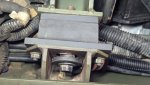
And now we have an air gap!:
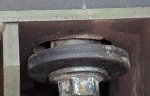
Fan to shroud clearance before and after. Seems to have raised the engine about 1/4-3/8"
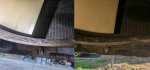
And the difference is noticeable. Lower cab noise and vibration. Especially at and near idle and just off idle when accelerating. When coming to a stop in gear I would have varying amounts of vibration depending on how the truck was sitting and where gravity was putting the most load on the collapsed mounts and sleeves I assume. No longer get that and much less vibration overall under all conditions. Very worthwhile.
Look close. I bet you ALL find yours are essentially the same unless you have already changed them.
2008 M1079 w/25,000 miles.
Before. You can see the "fretting" from vibrations that is causing that characteristic red "dusty" look. That's from constant abrasion of the metal that is shedding bits of iron and abrading the oxide layer. You can also see some cracking where the rubber is delaminating from the steel plates.
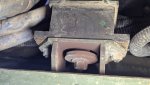
You can see that the safety sleeve that protects the bolt is eating it's way into the frame mounting bracket:
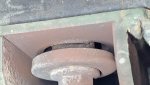
Changing these involves taking the upper fan shroud loose, unbolting the mounts, then lifting the engine up. I could only get about 1.5-2", and unlike the TM's suggestion of "remove the mounts" I had to unbolt the frame mounting bracket lower bolt, and loosen the upper bolt to rotate the bracket and allow removal of the rubber mount, sleeve, and bolt.
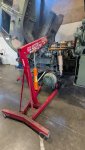
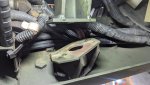
Old mounts and sleeves:
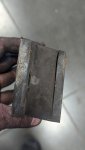
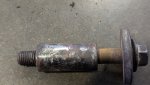
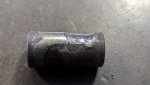
New mount installed:
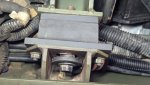
And now we have an air gap!:
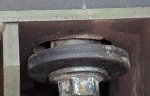
Fan to shroud clearance before and after. Seems to have raised the engine about 1/4-3/8"
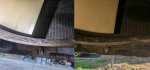
And the difference is noticeable. Lower cab noise and vibration. Especially at and near idle and just off idle when accelerating. When coming to a stop in gear I would have varying amounts of vibration depending on how the truck was sitting and where gravity was putting the most load on the collapsed mounts and sleeves I assume. No longer get that and much less vibration overall under all conditions. Very worthwhile.
Look close. I bet you ALL find yours are essentially the same unless you have already changed them.
Last edited: