VICTORY!!!!!
While explosives and tug of war were both great ideas and very satisfying entertainment wise I just couldn't get over the risk of potential energy turning into kinetic energy and launching a heavy piece of something to somewhere it shouldn't go. After a few days away from everything up in the mountains, my dad and I evolved several thoughts into a winning idea.
Upfront I'll apologize for not having a complete set of pictures. The excitement and success of our approach had our minds focused on getting both rotors pulled instead of documenting them. However, I think the idea is properly shown in the two pictures.
So we built a "pusher" tool to separate the rotor from the flywheel. The bar is 2"x2"x0.25 with a long Grade 8 3/8" bolt that will thread into the end of the rotor. The two square tubes are just there to help set up the contraption with the proper alignment. 2 4ton bottle jacks are then used as the "pushers". One picture shows the push bar, the other shows an after shot after our first rotor popped loose. You can see the red bottle jack is still mostly in the original place, while a yellow bottle jack has fallen out. 2x4's were stacked to get real close to the rotor so it didn't drop.
In all my previous attempts, I estimate I was able to apply ~400lbs static force, which didn't make it budge. The first rotor we tackled came off pretty easy actually, we "barely" started feeling any force on the jack pumps and it popped off. On the second rotor we pulled( the original one that started this mess ) we had to use significantly more force, I started to see some bow to the 2"x2" steel. I'm not a structural engineer, but its clear that some good amount of force would need to be used to bow a 2x2x0.25 piece of steel over a 13" span. Inspecting the rotor adapter plate and fly wheel did not show any clear reason why they were soo stuck. There was only a couple of very mild & small surface rust spots. No obvious paint bonding, adhesives, etc. So... the root cause remains a mystery.
No its time to start building a working MEP out of the pieces. I already have a NOS engine ready to go, so that should take care of the bulk of the initial problems with these sets. It wasn't my intent to have a super big project on getting a functional MEP, but once I start its hard to give up and admit defeat.
Thank you to all who have suggested ideas and followed along for sympathy.
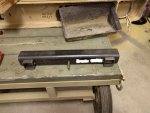
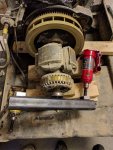