It's been a couple years since I updated this thread, but my M1031 is still my favorite truck and I've made a few more upgrades. I've gotten the generator to work reliably and have been focusing on the air compressor and lights. I always seem to be working on stuff when it gets dark and the box can get very dark. I tried some cold cathode compartment lights like you would find on a fire truck, but they just didn't put out the light. I finally ended up building a frame to flush mount some grote LED dome lights like you might find on a bus.
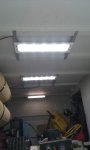
Towards the front of the truck you can see one of the older lights I tried. I do still use those in the large compartments where the generator control panel is and am going to put another in the welding torch side.
I liked AndyC's suggestion about adding an air brake tank from another truck.
My truck was missing the whole air compressor setup when I got it. The air tanks are great because they are aluminum so they're lighter weight.
Here's a picture of the whole side of the truck.
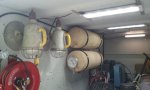
I used 1/2" air brake line to plumb in all the tanks and regulators. My air compressor is a fire sprinkler system compressor. It would only let me turn the air up to about 70, but I changed out the pressure switch and now it runs 100-120psi. It has ok flow but not like a shop air compressor. I've had this Sullair ES-5 compressor in the back of the truck for a while now. I've just gotten around to working on it. It's the smallest electric rotary screw compressor I've seen.
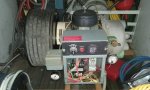
I added a 30 amp breaker to the panel and a 30 amp 3 phase 5 wire outlet.
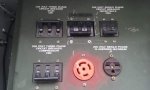
I've tried powering up the compressor a couple times but it seems to blow the 30 amp breaker sometimes. I'm curious if any of the electrician gurus out there can give me some advice. The compressor has a 9 wire motor and was originally wired for 480v. I changed it to a low voltage WYE configuration (T4-T5-T6 tied together, T7-T1 to L1, T8-T2 to L2, T9-T3 to L3). Would that be appropriate for the generator in the truck or should it be wired in a delta?