4 years ago I replaced my batteries with Walmart brand U1R lawn tractor batteries. Yesterday they were too weak to start it on test day so I figured I would just go ahead and replace them. My generator sits stationery so I have no need to tie them down.
I gave up trying to keep a charger on it since I test it under load once a month anyway. I figure if they won't hold a charge for a month they need replacing anyways. I have to turn the dead crank switch off or they will drain.
I did go a little more proper this time and cut the old ends off and put on some proper ends for the type battery I am using. I picked up some copper connectors for 4 gauge cable with 1/4" eyes. The eyes had to be reamed a little. I used 1x3/4" SS bolts with flat washers and lock washers. I bought the connectors at Tractor Supply.
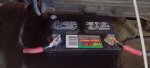
I gave up trying to keep a charger on it since I test it under load once a month anyway. I figure if they won't hold a charge for a month they need replacing anyways. I have to turn the dead crank switch off or they will drain.
I did go a little more proper this time and cut the old ends off and put on some proper ends for the type battery I am using. I picked up some copper connectors for 4 gauge cable with 1/4" eyes. The eyes had to be reamed a little. I used 1x3/4" SS bolts with flat washers and lock washers. I bought the connectors at Tractor Supply.
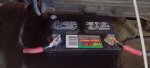