rattlecan6104
New member
- 357
- 7
- 0
- Location
- Oak Harbor, WA
So, its been a while since I have posted here, life gets busy and all that fun stuff. For a bit of a recap, I had recently done an engine swap with a "good used takeout" last summer. I had stripped it down to the block and heads and put my external components on it. Long story short, I should have looked more closely into the engine while I had it apart.
While I was attending trucking school during my college spring break(I am working on my ATA degree in diesel technology) I was doing a scrap metal run along the way, and heard that heart sinking knock. We parked it there until I was given the OK to take it to the college and work on it in the diesel class. The truck was still capable of moving under its own power, but I didn't want to risk further damage, so we decided to move it with a tow bar. The trucking school didn't have a tow bar that would work "properly" so we got creative.... very creative. We hooked the tow bar to the front of one of the school trucks and using a couple shackles hooked the other end to the pintle on the back of the deuce. I was behind the wheel of the deuce and my instructor was behind the wheel of the school truck pushing me across town, while still hooked up to a trailer. After this stressful ordeal, I strongly recommend not going this route, there is just way too much that could go wrong, but on the up side, the deuce felt amazing with that 435HP Detroit series 60 pushing it through town!
Moving on! We got the deuce into a stall and dropped the oil pan with an idea where the noise came from. It had spun the #1 con rod bearings. we were hoping for a wrist pin so we could do an in-frame rebuild, but no such luck. We pulled the engine, then ripped it apart looking for exact signs of failure. Three things were noted as we did this, #1, all the "friction" surfaces seemed to have quite a bit of wear, a couple coolant passages towards the front of the block were plugged, and engine oil was a gallon low. The engine had developed some leaks, so I knew about the oil level, every two weeks I needed to add about a gallon to begin with.
Trying to keep things on the cheap I utilized all potential parts I had available, I had two "junk" or "parts" engines and decided that since I spun the rod bearing I would want a replacement rod, then I saw that some of the pistons were different styles, so to prevent any unwanted mismatching I pulled a complete set of pistons, rods, and liners that were in usable condition out of one block for use in this current one. Then after looking at all of my cranks, it turns out that my other spare engine had the best crank, so I used that one. This project is still a work in progress, and at the moment I have $1500 invested in this, that's crank mag and polishing, main and rod bearings, new rings, and a gasket rebuild set. I'm hurting for both time and cash as is, so an LDS build, or a Cummins swap is just out of the option.
As I look through the TM's I am left with one potential question. Our college does not have an engine dyno that will hook up to this engine, so I cant do the recommended run in procedures. We have been taught that a feasible alternative is to essentially load the rig and run it. We have a test track, so this is safely doable, but the question remains is how? should I try to follow the procedures using gears to simulate approximate loads and time frames, Run half the day at approx half load or should I just load her down and "flog" her?
'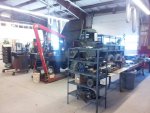
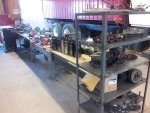
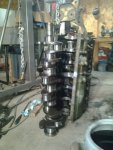
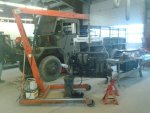
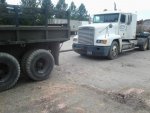
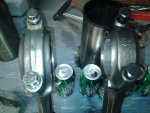
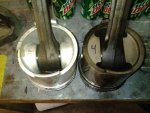
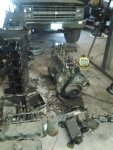
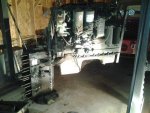
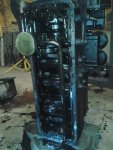
While I was attending trucking school during my college spring break(I am working on my ATA degree in diesel technology) I was doing a scrap metal run along the way, and heard that heart sinking knock. We parked it there until I was given the OK to take it to the college and work on it in the diesel class. The truck was still capable of moving under its own power, but I didn't want to risk further damage, so we decided to move it with a tow bar. The trucking school didn't have a tow bar that would work "properly" so we got creative.... very creative. We hooked the tow bar to the front of one of the school trucks and using a couple shackles hooked the other end to the pintle on the back of the deuce. I was behind the wheel of the deuce and my instructor was behind the wheel of the school truck pushing me across town, while still hooked up to a trailer. After this stressful ordeal, I strongly recommend not going this route, there is just way too much that could go wrong, but on the up side, the deuce felt amazing with that 435HP Detroit series 60 pushing it through town!
Moving on! We got the deuce into a stall and dropped the oil pan with an idea where the noise came from. It had spun the #1 con rod bearings. we were hoping for a wrist pin so we could do an in-frame rebuild, but no such luck. We pulled the engine, then ripped it apart looking for exact signs of failure. Three things were noted as we did this, #1, all the "friction" surfaces seemed to have quite a bit of wear, a couple coolant passages towards the front of the block were plugged, and engine oil was a gallon low. The engine had developed some leaks, so I knew about the oil level, every two weeks I needed to add about a gallon to begin with.
Trying to keep things on the cheap I utilized all potential parts I had available, I had two "junk" or "parts" engines and decided that since I spun the rod bearing I would want a replacement rod, then I saw that some of the pistons were different styles, so to prevent any unwanted mismatching I pulled a complete set of pistons, rods, and liners that were in usable condition out of one block for use in this current one. Then after looking at all of my cranks, it turns out that my other spare engine had the best crank, so I used that one. This project is still a work in progress, and at the moment I have $1500 invested in this, that's crank mag and polishing, main and rod bearings, new rings, and a gasket rebuild set. I'm hurting for both time and cash as is, so an LDS build, or a Cummins swap is just out of the option.
As I look through the TM's I am left with one potential question. Our college does not have an engine dyno that will hook up to this engine, so I cant do the recommended run in procedures. We have been taught that a feasible alternative is to essentially load the rig and run it. We have a test track, so this is safely doable, but the question remains is how? should I try to follow the procedures using gears to simulate approximate loads and time frames, Run half the day at approx half load or should I just load her down and "flog" her?
'
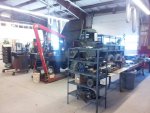
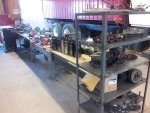
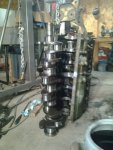
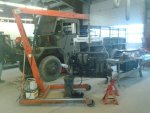
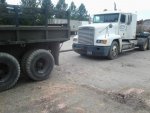
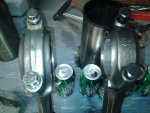
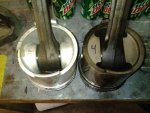
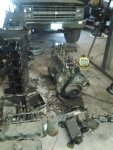
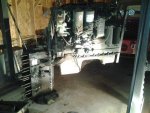
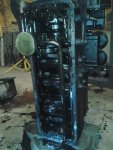