Thanks Guyfang for the "simple Governor setup and adjustment instructions", going to be using that soon. I have completely reassembled the gen set, I ended up changing the fuel return line to a 3/16" line. Wanted to change to a more common fuel line size and I had it on hand, bought some fitting need for change.
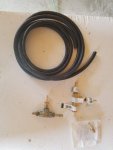
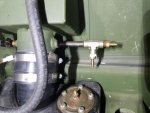
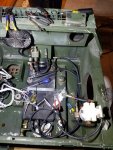
I replaced the filters on the pumps as well, and replaced the oil pressure switch due to it leaking. Fuel level switch was replaced too, the low fuel was not working on the float. I cleaned out the frequency converter as well.
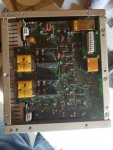
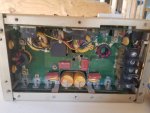
After I had it all put back together I pulled out the PMCS check list. I reattached the battery and disconnected the primary fuel pump. Hooked up aux fuel to a fuel can and filled tank to about 1/2 after that, I reconnected the primary fuel pump and observed for leaks. I allowed this to prime for about 5 mins, during this process i was going threw check list. Turned it over fired right up, governor system needs some adjusting kinda likes to surge a bit. This is to be expected after pulling the engine, I went ahead and allowed the unit to run for around 10 mins. Then I applied a 2800 load to see if it will hold the load, it holds it the load. Now to the remaining issue this was present before the tear down, when under load it puts out black smoke. The TMs says:
18. ENGINE EMITS BLACK SMOKE (Unit-Level Troubleshooting)(TM 9-6115-639-13&P*)
Black smoke is emitted from exhaust pipe.
Troubleshoot in accordance with TM 9-2815-257-24.
Note: before i jump to that TM lets see what Direct Support Level says.
8. ENGINE EMITS BLACK SMOKE (Direct Support Level Troubleshooting)(TM 9-6115-639-13&P*)
a. Check for clogged, sticking, or worn fuel injector nozzle.
b. Check fuel injection timing.
Adjust in accordance with TM 9-2815-257-24.
8. ENGINE EMITS BLACK SMOKE (Unit-Level Troubleshooting)(TM 9-2815-257-24)
a. Check for clogged or dirty air filter. Remove and replace air filter (Para. 3-16).
b. Check for clogged, sticking, or worn fuel injector nozzle. Remove and replace fuel injector (Para. 3-14).
c. Refer trouble to direct support maintenance level.
Air filter is clean as can be, brand new.
7. ENGINE EMITS BLACK SMOKE (Direct Support Level Troubleshooting)(TM 9-2815-257-24)
a. Check injection timing (too slow) (Para. 4-11). Adjust fuel injection pump timing by removing shims (Para. 4-11).
b. Refer trouble to general support maintenance level.
After reading that seem like it points to an injector issue. Looks like I'm going to watching some Youtube on how to check a injector. The fuel I'm using is
Diesel #2 around 8 months old, no treatment. Any help would be greatly appreciated.