mclarkva
New member
- 14
- 0
- 0
- Location
- Charlottesville VA
Been around this for awhile - operated for a while with bars leaks radiator sealer with radiator cap off so no pressurization.
trapped water is rusting things under valve cover - broken spring on #4
Going to have to tear it down!
Anybody have one of those special head bolt wrenches to get to the head bolts Under the lifter rail?
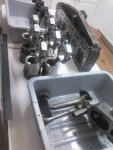
trapped water is rusting things under valve cover - broken spring on #4
Going to have to tear it down!
Anybody have one of those special head bolt wrenches to get to the head bolts Under the lifter rail?
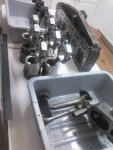